MAJOR WATER REDUCTION
Water required to properly cool off Sage panels can be reduced by more than 50% to all features described below.
More effective insulation that allows a smaller amount of heat to be transferred to the water.
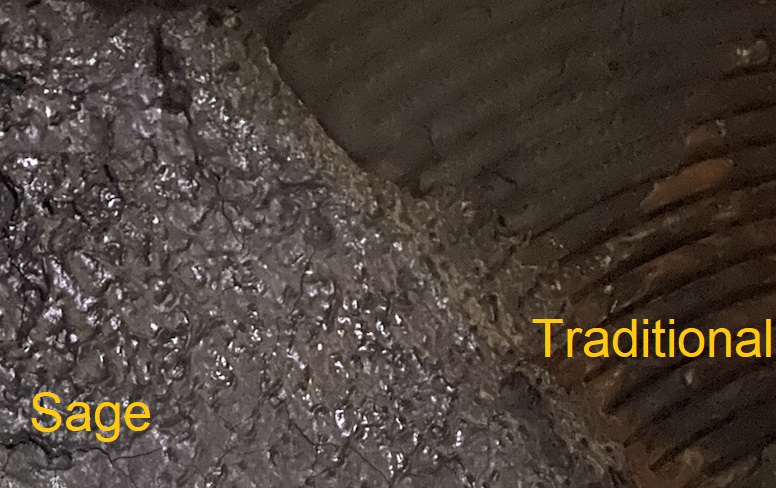
Sage Panels are designed either to maximize heat flow (panels beyond the furnace) or to maximize retention of heat inside the furnace in roof and shell panels
At left one can see the difference.
optimized insulation
no exposure to direct radiation
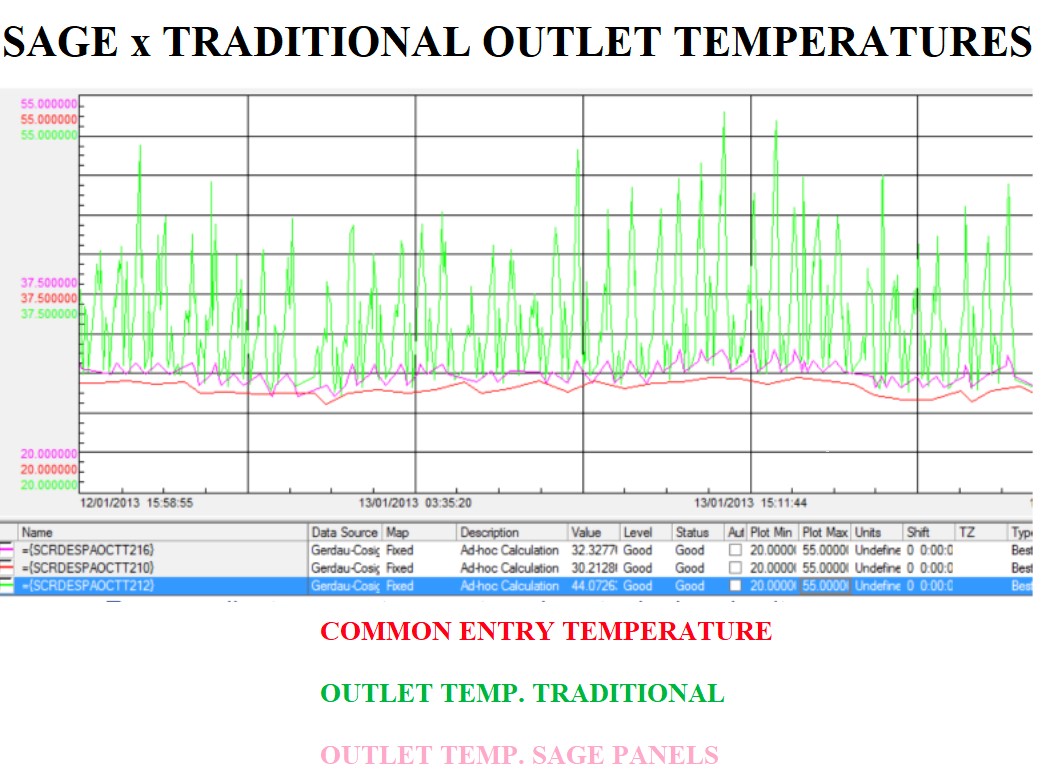
EFFICIENCY OF THERMAL SHIELD
The 1” thick shield composed of fins designed to withstand oxidizing or reducing or abrasive atmosphere, maximize refractory life which in turn maximize fins life cycle.
Two panels with same heat input had the outlet water temperature measured to demonstrate the efficiency of the insulation of Sage panels. Results at left
Cooling Water Temperature in EAF Roof
The graph at left shows not only the variation of water needs in different panels, but also that peak demand for water only occurs only during 1/3 of the power on.
Only Sage Panels are fed in accordance to their real need in real time.
Unnecessary expenses with water collection, treatment, circulation and cooling adds to the huge amount of heat removed from the furnace that will demand more energy to be cooled off.
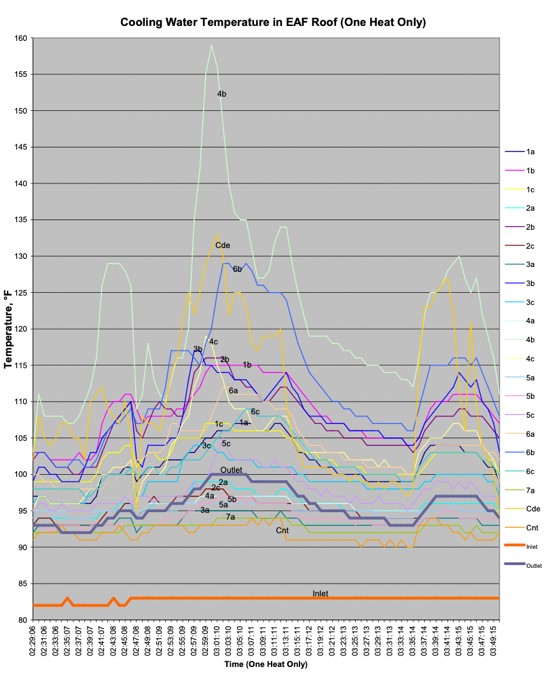
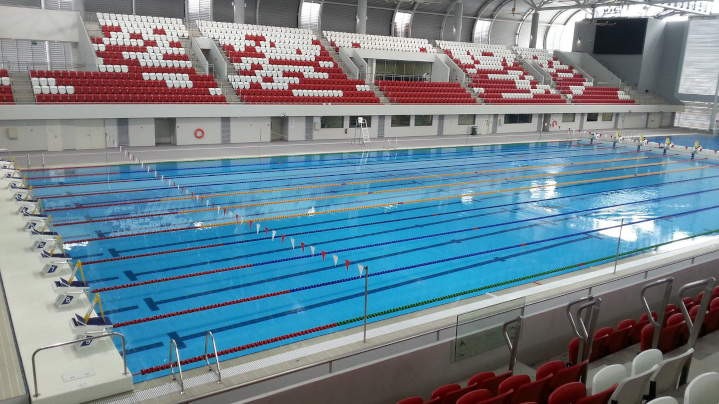
typical EAF
A typical EAF with 100 ton capacity, circulates in the furnace panels during one day, between 3 and 5 times the volume of an Olympic Swimming pool.
More than 50% UNNECESSARILY
DIRECT MEASUREMENT OF HOT FACE TEMPERATURE
Sage panels are the only ones in the industry, capable to measure and record temperatures at the hot face of panels in real time.
Thermocouples are inserted under a permanent layer of refractory in direct contact with the tube metal.
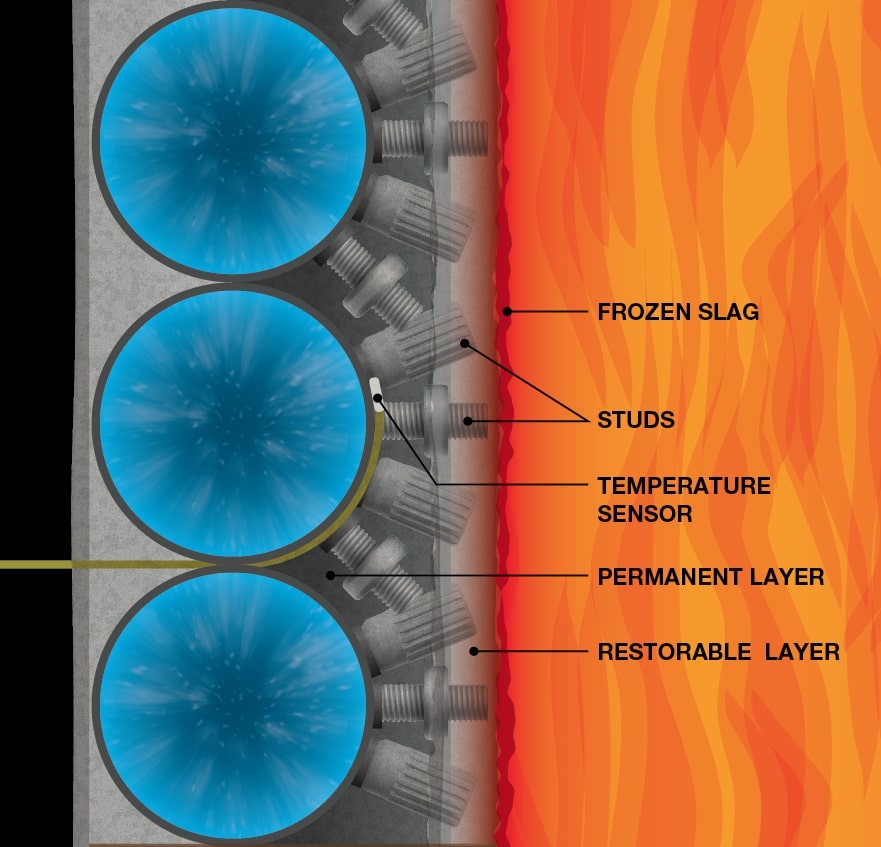
SAGE INSTRUMENTED PANELS + AUTOMATED VALVES CONVERT THESE TRADITIONAL FLAWS INTO CASH.
Sage panels are the only ones capable of triggering the overheat alarm based on real time temperature readings directly from the hot face. Thermocouples installed under a permanent insulating layer, store data about the safe range of flows required by each individual panel.
Thermally activated valves respond in real time to the needs of each panel.
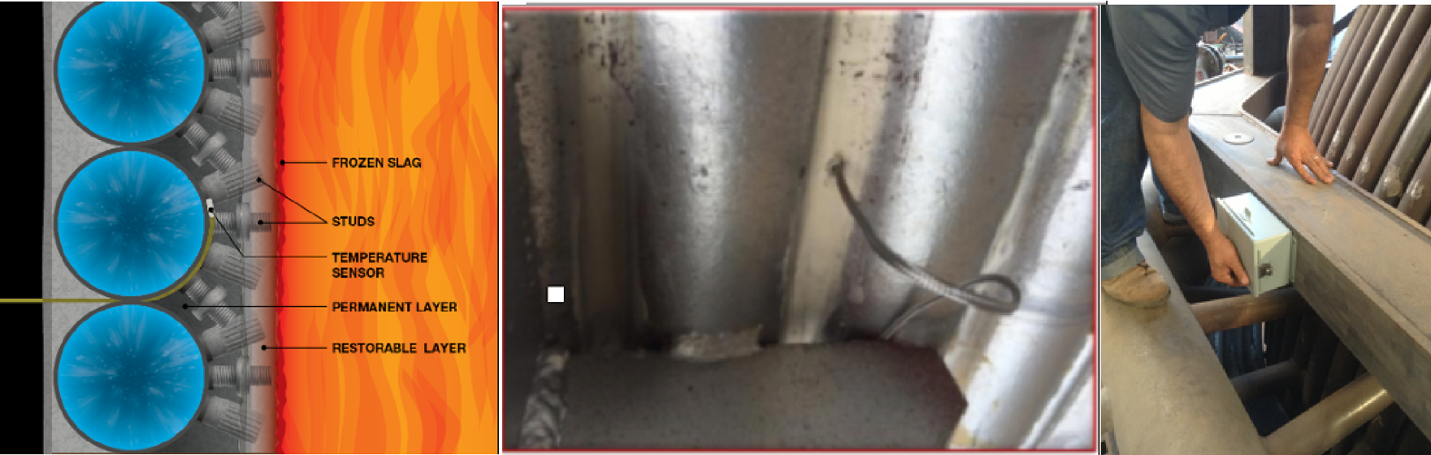
That results in safe water reduction with cascading savings in collection, chemical treatment, circulation and cooling.
Flow in traditional panels is defined by that required by the most demanding panel. That results in more than 50% of unnecessary flow and does not prevent furnace disarming.
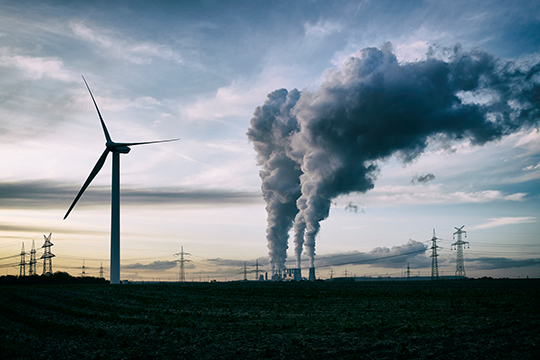
EMISSIONS REDUCTION
MINIMIZED AIR INFILTRATION.
Air infiltration has been traditionally disregarded. At the temperatures prevailing in EAFs, nitrogen is oxidized forming NOx. Sage seals all points of infiltration between panels and through the slag door.
Around 80% of air is Nitrogen. A 100tons/run EAF takes in between 120 and 150 kg or air per ton. Beyond the huge environmental damage these emissions will soon be taxed.
SELF FOAMING SLAG
Sage Self Foaming Slag reduces all emissions generated during the primary refining stage to less than 50% of what is generated by Oxygen and Carbon injection.
This approach is part of the production cost reduction without investment and must be discussed after a non disclosure agreement is signed with interested prospects.
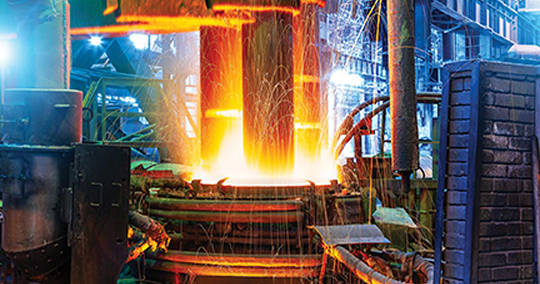